Peter Søe Nielsen from DTU Mechanical Engineering defends his PhD "Analysis and Optimisation of Carcass Production for Flexible Pipes" Wednesday, 14th January 2015 at 13:00. The defence takes place in Building 101, Auditorium no. S09, at the Technical University of Denmark. Principal supervisor is Professor Niels Bay.
Un-bonded flexible pipes are used in the offshore oil and gas industry worldwide transporting hydrocarbons from seafloor to floating production vessels topside. Flexible pipes are advanta-geous over rigid pipelines in dynamic applications and during installation as they are deliv-ered in full length on reels. Flexible pipes are constructed in a layer structure in which each layer adds specific properties to the pipe such as; collapse strength, fluid integrity, bursting strength, tensile strength etc. The inner-most layer of a flexible pipe is the carcass; a flexible interlocking stainless steel structure that provides mechanical and collapse strength for the flexible pipe. The manufacturing process of carcass is a combination of roll forming stainless steel strips and helical winding the profiles around a mandrel interlocking the profiles with themselves.
The focus of the present project is the analysis and optimisation of the carcass manufacturing process by means of a fundamental investigation in the fields of formability, failure modes / mechanisms, Finite Element Analysis (FEA), simulative testing and tribology.
A study of failure mechanisms in carcass production is performed by being present at the production floor when such incidents arise, the so-called ‘Gemba’ methodology. The outcome is a list of general failure mechanisms in the carcass process and it is noted that most issues are encountered in the winding stage.
Issues with carcass profile geometry is a recurring event and it was found that the degrees of freedom which the carcass profile experiences during interlock winding allow the profiles to minimise stresses and strains during winding by adjusting the profile geometry – the effect being more pronounced with decreasing mandrel size.
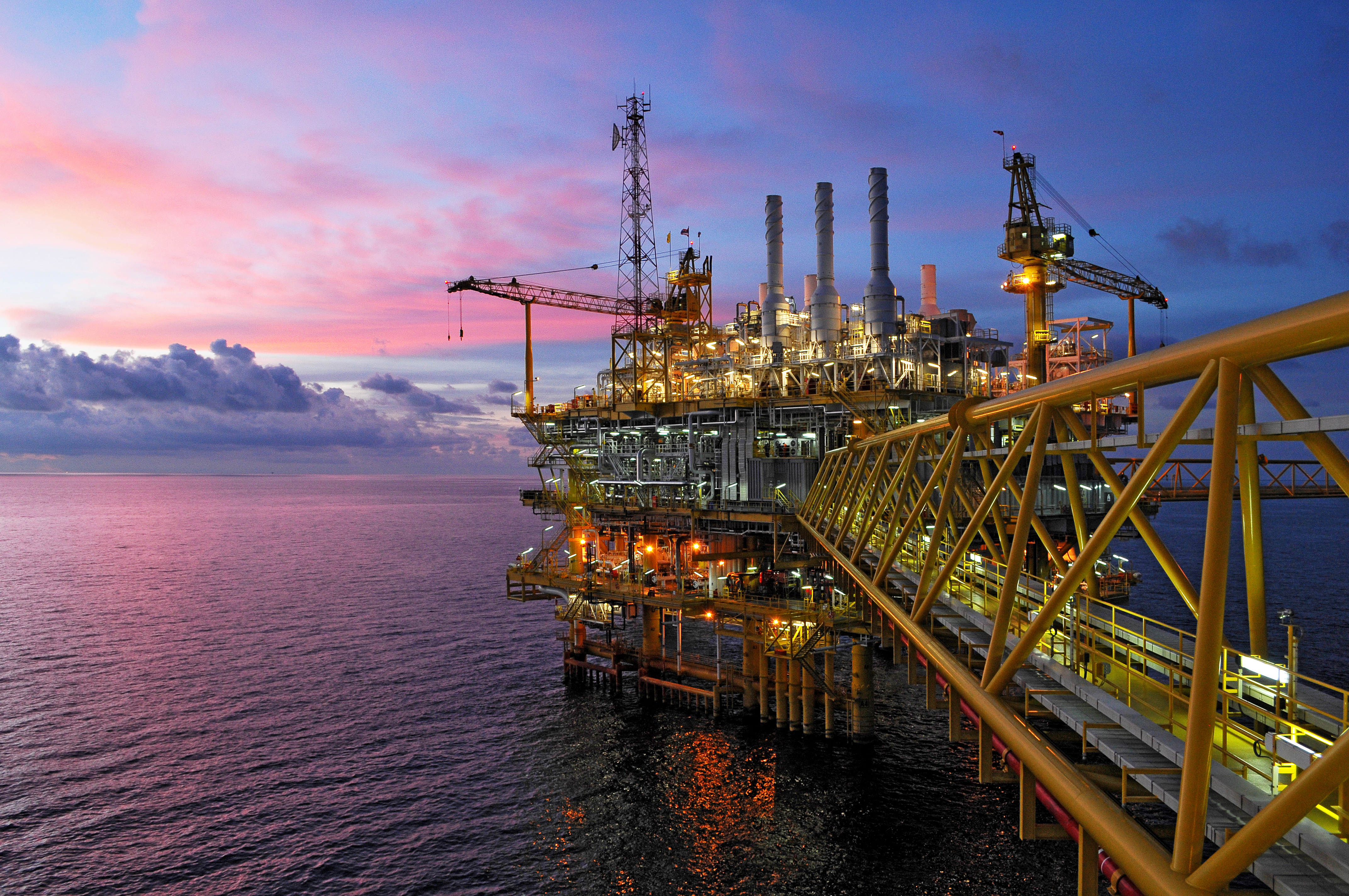
Photo: Colourbox
This effect was effectively accounted for by changing the profile geometry in the roll forming stage. LS-DYNA® is successfully used to construct simple winding models and a three-point-bend using shell elements. A convergence study is performed to ensure parameters for numerical stability. The simple winding models were in agreement with production measurements and they were successfully used in evaluation of weld relief-cut functionality. The three-point-bend FEA indicates possible problems with the shell elements when boundary conditions allow free-forming.
A simulative three-point-bend test is constructed to simulate profile tongue strains during winding. Preliminary testing shows promising results but problems in obtaining similar boundary conditions to the profile as in winding needs to be resolved. In the simulative test simple v-bent profiles shows comparable to roll formed profiles and seems to be a viable op-tion for fully offline simulative testing of weld and weld relief-cut fracture.
Material characterisation of one austenitic and three duplex grade stainless steels is performed (EN 1.4404, EN 1.4162, EN 1.4462 and EN1.4410). Flow curves and anisotropy values are attained but problems with notched tensile specimens meant that only uni-axial tension FLC points were attained.
Analysis of weld fracture of duplex stainless steel EN 1.4162 is carried out determining strains with GOM ARAMIS automated strain measurement system, which shows that strain increases faster in the weld zone than the global strain of the parent material. Fracture in the weld zone occurs at an average global strain of 0.1 where the average fracture strain in the weld zone is 0.27. The reason is explained by lower hardness in the weld zone compared to the parent material.
Weld fracture can be suppressed with introduction of weld relief zones. However, production strain measurements and FEA analysis showed that cutting a relief zone creates high strains locally in the relief-cut itself – more than a factor two larger than the nominal highest strains elsewhere in the profile. Weld relief-cuts are optimised by moving the relief-cut next to the weld seam and only cutting 1 x strip thickness deep.
Simulative tribo-testing in the strip-reduction-test showed that biodegradable rapeseed oil is an acceptable lubricant for the carcass process. Testing of two lean duplex stainless steel sur-faces showed that a EN 2E brushed surface had better lubricant entrapment capabilities than a EN 2B bright annealed surface.
Swarf was found to originate from either strip edge in contact with the forming tool or with another strip edge during interlocking or from pickup abrading the strip surface. An increase of tool curvature in contact with the strip edge is shown to have a positive effect on edge swarf.
Pickup was seen as an issue on the roll forming tools but it does not develop past a certain amount. It is, however, continuously formed and removed thus resulting in adhesive wear on the tools. The result, combined with cyclic contact loads, is tool failure by chipping.
Tribo-system performance was greatly improved by the use of an AlCrN tool coating. Unlike normal polished tools, where pickup on the tools is seen from less than 80km production, the coating enabled production of more than 650km EN 1.4162 stainless steel strip without any pickup forming or tool chipping.