Ole H. E. West from DTU Mechanical Engineering defends his PhD "Failure Analysis and Thermochemical Surface Engineering of Bearings in the Wind Turbine Drivetrain" Thursday, the 15th of January at 13.00. The defence takes place in Building 101, Meeting room no. S12 at DTU Lyngby.
Abstract
A critical premature failure mode of rolling element bearings inside the wind turbine drivetrain is associated with the formation of so called white etching cracks (WECs). So far there is no consensus on the root cause of WEC failure and the exact influence of different drivers and their combinations is not well understood.
Various types of failed rolling element bearings from different positions inside the wind turbine drivetrain were investigated. Both conventional techniques as reflected light microscopy (RLM), scanning (SEM) and transmission (TEM) electron microscopy as well as electron backscatter diffraction (EBSD) and ion channelling contrast imaging (ICCI) were used. The gap between RLM and SEM (providing a good overview over the crack morphology) and TEM (providing very detailed information but from a very limited part of the sample) could be covered by the use of EBSD and ICCI. Different occurrences of WEC failure were observed and a detailed characterization of the crack morphology and morphology of white etching areas (WEAs) bordering the cracks was possible, allowing assumptions on WEC formation and propagation.
In addition a RCF testing method was developed using hydrogen charged rollers to reproduce WEC formation. The influence of different hoop stress levels was studied. The fracture surfaces as well as formed WECs were investigated. A detrimental effect of higher hoop stress levels on roller lifetime was found and based on the analysis of the formed WECs an incremental increase of WEA formation with each cycle was suggested. By X-ray diffraction stress analysis the non-uniform build-up of compressive stresses under testing was identified.
Deep nitriding is considered as a potential remedy against WEC failure. Therefore nitriding experiments were conducted to study the influence of different alloying concepts, prior heat treatments and nitriding parameters on the case properties. With optimum nitriding conditions a maximum nitriding depth of 800 µm was achieved, without formation of a thick porous compound layer. The build-up of near surface compressive stresses was confirmed by synchrotron X–ray diffraction stress analysis. The performance of surface engineered rollers was evaluated by RCF testing under conditions that are known to provoke failure in rollers made from a standard bearing steel. One of the nitrided materials showed promising results.
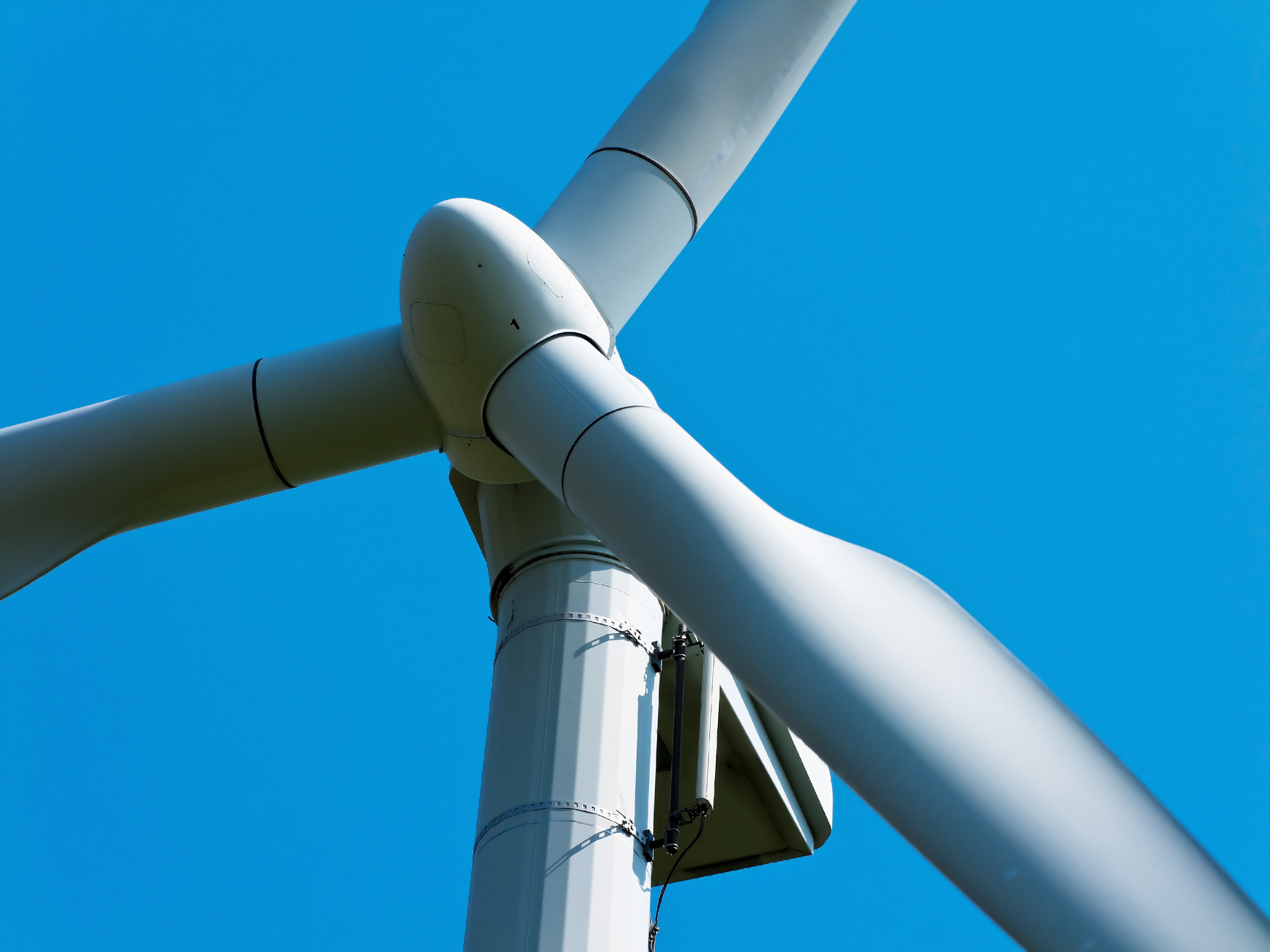
Photo: Colourbox.