Section of Materials and Surface Engineering
The Section of Materials and Surface Engineering's core competences lie within microstructural engineering through thermo-mechanical, thermo-chemical and electrochemical processing as well as advanced characterization of microstructures, materials properties and performance.
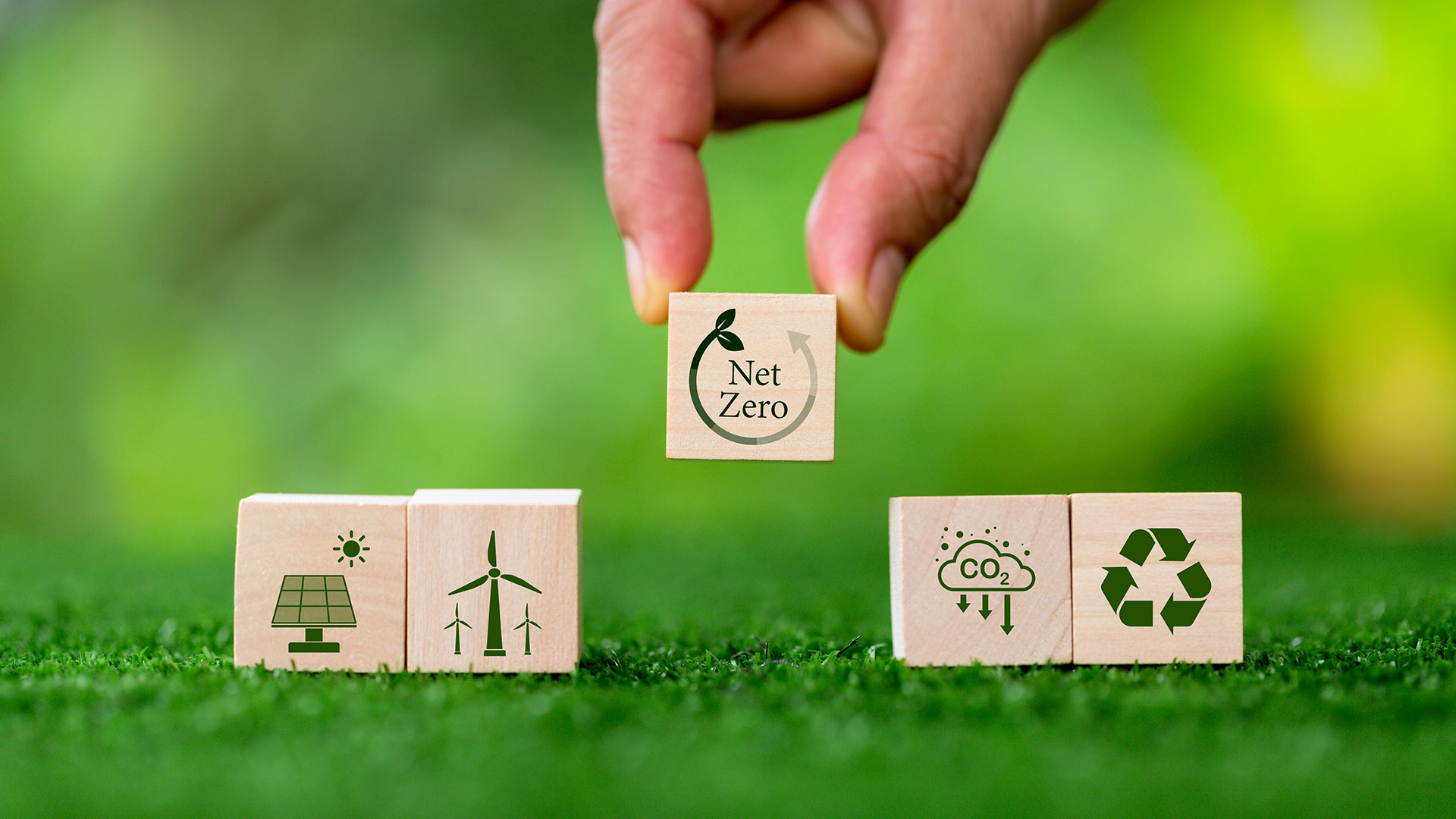
These competences are augmented through close interaction between experimental and modelling activities, incl. Integrated Computational Materials Engineering, fostering the fundamental understanding of phase transformations, microstructure evolution, corrosion phenomena and micromechanics.
The section’s multidisciplinary activities span over all length scales and cover the entire engineering value chain, often in collaboration with industry.
The strategic areas include:
- Enhanced material durability through microstructure and surface engineering to improve resistance against e.g. wear, fracture, fatigue, heat, corrosion in aqueous, gaseous and high-temperature environments
- Robustness of electronics, incl. power electronics, exposed to humidity
- Innovative multifunctional materials, integrating electrical, thermal and mechanical properties
- Reduction of CO2 emission by novel processing of metallic or cementitious materials or CO2 capture
- Materials and processes for future advances in Power-2-X and nuclear energy
- Sustainable materials and processes for recycling and remanufacturing
Contact
Grethe Winther Head of Section, Professor Phone: +45 45254755 Mobile: +45 93511691 grwi@dtu.dk